国内汽车产业链上的一个“卡脖子”技术难题,由一家渝企取得重大突破!我国较大的专业汽车变速器企业之一——重庆青山工业有限责任公司(简称“重庆青山”),自主开发出7挡DCT(双离合变速器)液压模块,搭载于国内一大型车企的产品上,成功实现量产。
12月24日,来自重庆青山的新数据显示,9-11月,该液压模块已生产2万台,搭载于众多汽车上,整车驾驶性表现优异。这标志着重庆青山自制液压模块项目赢得市场认可。
以“卡脖子”技术为突破口
一直以来,DCT自动变速器的核心零部件总成——液压模块基本被外企或合资企业垄断,卡住了国内变速器企业及整车企业的“脖子”。
关键核心技术,是要不来、买不来、讨不来的。怎么办?
重庆青山决定就在这种“卡脖子”的地方狠下功夫,自主研发液压模块,提升创新突破能力,从根本上改变关键核心技术受制于人的局面。
2019年3月,重庆青山对此立项。随即,一次次高层会议研讨自制液压模块项目的资源调度与研发进展;集中优势资源,新建1台液压高低温综合功能试验台,1台振动试验台、1台温度冲击试验台,解决研发硬件“瓶颈”;集中企业技术骨干,由企业技术带头人领军,组成专项研发团队,并划拨专项资金;各环节通力合作,为自制液压模块的技术研发、试验验证、样件试制、整机装配、批量生产提供合力……
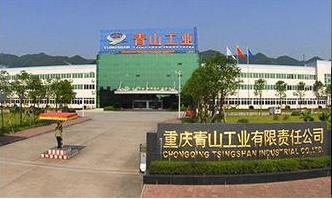
创下开发时间短纪录
既然是“卡脖子”技术,要攻克它,必然较为艰难。
2019年10月,液压模块试验进入关键时期。每一组数据的出炉,工程师邹敢都寸步不离地守在试验台架边,短则三五天,长则半个月。
为了赶进度,通常是几个试验台架一起上。DV测试数据、软件逻辑数据、整车标定数据……一组组的数据就好似邹敢的孩子,他不分白昼地等候孩子们的降临。那段时间,邹敢原本就不壮实的身材更加瘦弱了。
回想起液压控制模块A样开发的那段时间,技术骨干姜率仍然难以掩饰内心的激动——
那是在变速器总成换挡测试的过程中,出现一种“挤油声”,姜率与液压离合开发设计所的小伙子们一起,泡在试验中心。他们拟定了三种不同的方案,连夜进行低温、常温、高温测试,但效果并不明显。
“不如我们再次进行液压原理分析,从电磁阀入手,每一个特性逐一检查。”姜率提议。
正是姜率的这一大胆判断,终于打破了试验僵局,成功消灭掉“挤油声”。
在经历了长达两个月的苦战之后,所有技术问题终于被攻克!A样液压模块进入B样开发。
经过A样至C样的8轮样件开发,通过37项功能、性能与可靠耐久检测,涵盖-35℃至140℃温度环境测试;经过搭载国内两家主机厂共10余轮次的整车可靠性道路试验;经过夏季标定、冬季标定的反复验证……所有问题均得到充分暴露,所有问题均得到有效解决。
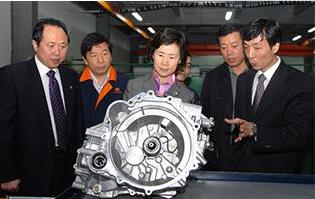
到2020年9月,自主液压模块终于实现量产。算起来,整个研发持续一年半——但这却创造了国内外同行中液压模块开发时间较短的纪录。
能替换国外产品吗?能!
这次自主开发,重庆青山是从“无”到“有”、从技术到产品的艰难历程。那么,能达到国产替代外企或外资产品的要求吗?
这得用户说了算,市场说了算。
专业人士评价,“重庆造”7挡DCT液压模块,采用全电液比例控制,系统控制精度与响应大幅提升,支持高响应的离合器与挡位控制;集成换挡电气驱动模块与传感器系统,成本降低,系统高度集成化;可靠性与寿命提升,抗污染能力增强。
而搭载这款产品的车企则表示,与国外和外资液压模块相比,“重庆造”在系统泄漏、换挡响应、模块重量等方面具有性能优势,且成本显著降低,市场竞争力更强。
“至此,这项关键核心技术终于牢牢地掌握在我们自己手里了,既保证了汽车产业链安全,也创造了新的竞争优势。”重庆青山相关负责人说。
文章来源: 重庆日报